With the rapid expansion of our country's green economy, mono crystalline silicon/poly crystalline silicon photovoltaic power generation and thin-film BIPV technology are maturing. Steel structures have significant advantages over other types of structures in terms of use function, design, construction, and overall cost. As a result, developing and manufacturing a new type of steel structure photovoltaic mounting system to replace the present angle steel mounting system is critical.
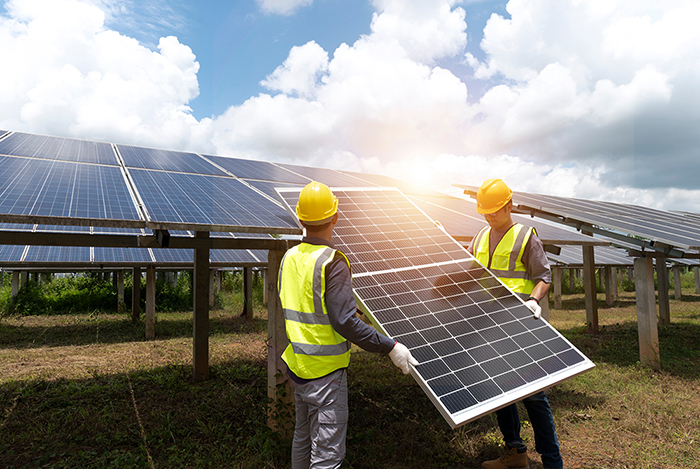
1. Steel type of solar steel bracket
Light-duty structural steel and small-section ordinary structural steel are currently utilized in the selection of steel due to the characteristics of simple structure and small volume of solar PV support.
Light structural steel: This term refers to round steel, small angle steel, and thin-walled steel. When angle steel is utilized as a supporting element, it may make effective use of steel's strength and is useful to the overall frame installation. At the moment, the national standard angle steel relative to the solar support, the optional model is few, so additional small angle steel models are needed to adapt to the current rapid development of the solar energy industry. Thin-walled steel purlins are typically made of 1.5-5mm thick thin-walled steel plates that is cold-formed or cold-rolled to make thin-walled steel products with varying cross-sections and diameters.
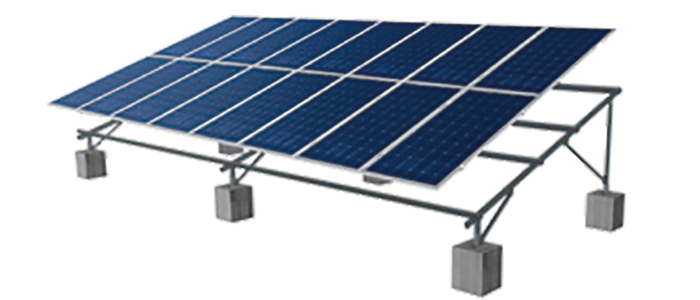
When compared to hot-rolled section steel, the rotation radius of thin-walled section steel can be increased by 50-60%, and the inertia moment and resistance moment of the section can be increased by 0.5-3 times, but because thin-walled steel is mostly processed in the factory, there is a need for high-precision drilling holes and photovoltaic panels after the screw hole. Because the steel section is small, tools are difficult to work, and construction is more difficult after the factory processing drill button, can hot-dip galvanising rust-proof, transport to the site installation. Currently, most household panels cannot be directly coupled with thin-walled steel installation and must be attached to another auxiliary fixed structure (such as a press block).
Photovoltaic frequently used generally contains I-type, H-type, L-type and varied design needs of profiled cross-sections, and is usually constructed of carbon structural steel or low alloy steel, which is easy to build and low in cost. The processing methods are also diverse, with the welding section steel being chosen with different thicknesses of steel plate, according to the design requirements in the factory welding processing shape steel, this forming method can be calculated according to the forces on different structural parts of the photovoltaic project, and the steel plate with different thicknesses can be used at different parts, which is more reasonable than the force on hot-rolled one-time steel plate.
2. The solar energy support steel material performance requirements, the steel material of the solar energy steel construction shall have the following performance:
1). Tensile and yield strength. A high yield point might decrease the section of steel members, reduce construction weight, save steel, and lower total project costs. High tensile strength can boost a structure's overall safety reserve and improve its reliability.
2). Toughness and fatigue resistance. Good plasticity can cause the structure to deform significantly before failure, allowing personnel to identify and implement corrective actions in good time. Good plasticity can also be used to adjust the local peak stress, the angle of the solar panel installation, the use of forced installation, and the plasticity of the structure to produce internal force redistribution, so that the structure or some components of the original stress concentration of the stress distribution of the structure tend to uniform, and improve the overall bearing capacity of the structure. Better toughness allows the structure to absorb more energy when it is destroyed by an impact load, which is especially important for desert power stations and roof power stations exposed to high winds. Better fatigue resistance can also make the structure more resistant to variations in the ability to withstand repeated wind loads.
3). The processing speed. Cold workability, hot workability, and weldability are all examples of good workability. Aluminium used in photovoltaic steel structures must not only be easily machined into various structures and components, but it must also be machined in such a way that the strength, plasticity, toughness, and fatigue resistance are not compromised.
4). Duration of service. Because the design life of a solar PV system is more than 20 years, good anti-corrosion performance is also an important indicator of the mounting system's quality. If the support life is too short, it will damage the overall stability of the structure, extending the payback period and reducing the overall economic benefit of the project.
5). In accordance with the preceding conditions, solar steel structure steel should be simple to purchase, manufacture, and sell.
3.Technical evaluation of new-generation solar steel structural supports
The use of angle steel solar energy support is currently subject to more and more conditions, the most important reason being that the quality of steel is uneven at the moment, installation requires a large number of on-site drilling, but after drilling the steel is easy to rust, so a new type of bracket is required to replace these angle steel brackets in order to slow down corrosion and extend service life.
The primary structure of the new solar energy support is as follows:
1). A system of special-shaped cold-formed thin-walled steel support structures. Special-shaped cold-formed thin-walled steel is a light-gauge steel structural system that can be fabricated in batches, built fast, and fully operational. The steel structure bracket of a special-shaped cold-formed thin-walled steel structure system is a type of steel structure frame made of prefabricated cold-formed thin-walled steel that is bolted together on the job site.
2). A factory-made monolithic steel mounting system. The prefabricated steel frame with purlins can be constructed and fixed on site before being combined with panels to form the entire PV array. The installation requirements of this steel structure bracket are quite high, the steel utilised is of the highest quality, the surface treatment process is good, and early communication with photovoltaic component makers is required to ensure a successful assembly.
3). Curtain wall photovoltaic support structure system with a beam-column frame. It is appropriate to use a beam-column frame steel structure mounting solution for PV curtain walls. Because of its low lateral stiffness, when the structure's or story's height is high, the lateral braces should be set to form the supporting frame structure. Steel structure and cast-in-place embedded elements are frequently utilised to produce a hybrid structure in the design of high-rise photovoltaic curtain wall, which can improve the anti-lateral ability of the entire structure while reducing the amount of steel required and therefore lowering the total cost.
4. Installation of new cold-formed thin-wall solar support components:
1). The innovative cold-formed thin-wall solar energy support for steel structure members is constructed in the factory using various steel-plastic mixed connectors. There are several varieties of steel-plastic mixed connectors that may adapt to diverse installation conditions.
2). The new cold-formed thin-wall solar energy support is lighter in weight and has more mounting holes. In general, the Independent Foundation is the primary foundation, with the reinforced concrete connection beam added as needed. Strip foundations or Cross Foundations can be employed in places with poor geological conditions, but Raft Foundations should be avoided as much as possible. The upper column bases are all hinged, while the embedded components are either inserted column bases or embedded bolts encased in waterproof concrete. Both types are simple to process, easy to build, and well-connected.